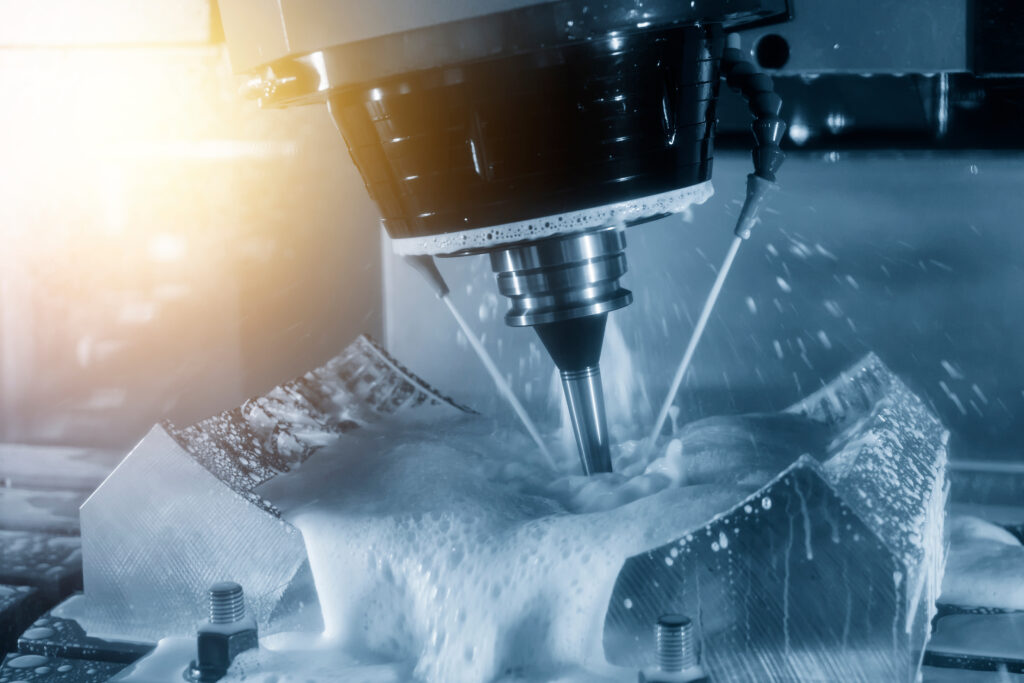
CNC milling, with its roots dating back to the mid-20th century, has evolved into a cornerstone of modern manufacturing. It relies on computer-guided precision to cut components from raw materials, enabling the creation of everything from intricate aerospace parts to custom firearm assemblies. The diversity of CNC milling machines ensures that there’s a machine tailored for almost any application, providing the industry with a versatile and adaptable tool for various projects. In this blog, we’ll discuss CNC milling, its numerous types and their applications, the benefits of choosing CNC milling for your project, ultimately arming you with the knowledge to optimize your manufacturing projects.
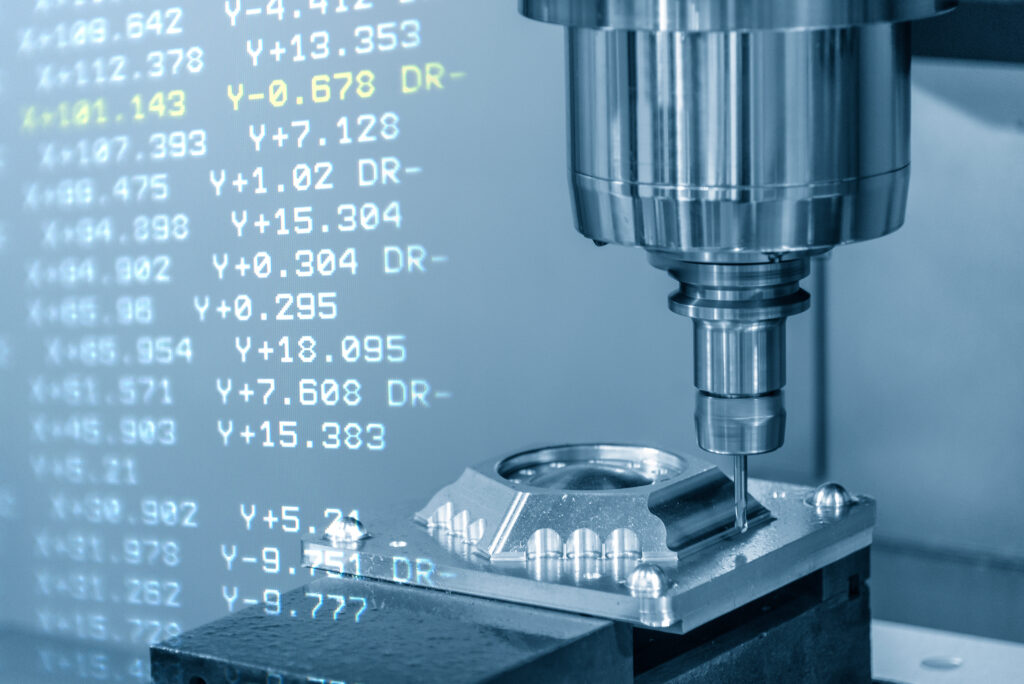
Precision.
CNC (Computer Numerical Control) milling is a sophisticated machining process that relies on computer programs, typically G-Code, to precisely control milling machines. These programs control critical parameters such as cutting speeds, feed rates, and tool paths, ensuring every operation is executed accurately. The versatility of CNC milling is unmatched, enabling the machining of almost any material, from metals and plastics to composites and exotic materials. Moreover, CNC milling machines can operate on different axes, allowing for intricate and complex geometries that would be challenging to achieve using traditional machining methods. The introduction of 3rd, 4th, or 5th axis milling machines has expanded CNC milling’s capabilities, making it ideal for industries like aerospace, medical, firearms, prototyping, and defense, where multifaceted components are standard.
When it comes to precision, CNC milling has set new standards, with tolerances as tight as 0.0005 inches now being the standard in world-class machine shops. This level of precision not only reduces the need for extensive post-processing but also elevates the overall quality of the end product. Reduced post-processing and improved quality are only two advantages of CNC milling. It also offers enhanced efficiency, as these machines can operate continuously with minimal human intervention, resulting in reduced production time and labor costs. The repeatability and consistency of CNC milling make it an invaluable tool for mass production, where identical designs must be replicated across multiple workpieces. As CNC milling continues to evolve, it has become a cornerstone of modern manufacturing, influencing various industries and allowing precision that was once deemed impossible to produce.
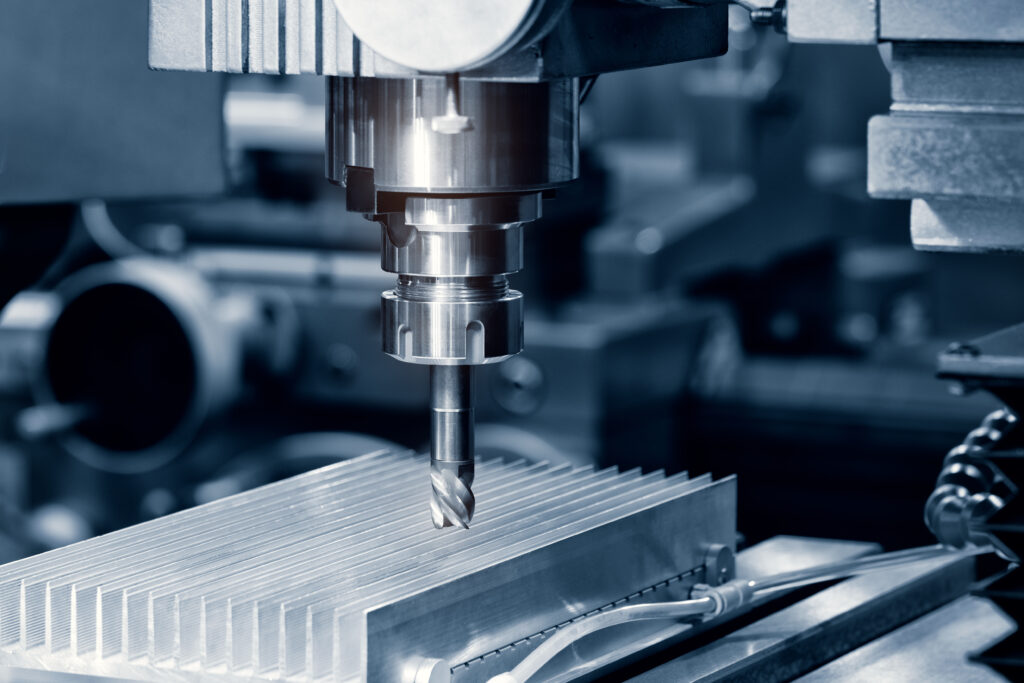
Efficiency.
The benefits of CNC milling are not limited to precision and complexity. The efficiency brought to the table by CNC mills is a game changer. As mentioned before, the need for labor-intensive handwork, & post-processing is drastically decreased when using a proper milling machine. Additionally, CNC mills excel in significantly reducing the time it takes to produce parts. They succeed in minimizing material scrap, & operating unattended for extended amounts of time. CNC mills were designed with efficiency in mind, the automated tool changing system is another component that will help drive productivity and cost-effectiveness across numerous industries. Rapid prototyping and design iteration are simplified thanks to the efficiency benefits, meaning that prototypes and testing can easily be completed before committing to mass production. Successful rapid prototyping allows for parts to be refined and optimized, meaning that mass production will be completed precisely, and timely. Ultimately resulting in successful production schedules, and optimized resource utilization. Not only are you able to machine more intricate parts, while holding tighter tolerances, CNC milling allows you to do all of it at a faster rate.
Complexity.
Arguably the greatest benefit unlocked by CNC milling is the unparalleled complexity. 3D features that would challenge the limits of traditional methods, not only become feasible with CNC mills, but highly repeatable as well. 5th axis milling provides the ability to machine at multiple angles & orientations, without the need for repositioning the part, this is a valuable, time saving capability for intricate, multi faceted parts. 4th and 5th axis milling has become essential for milling parts with multiple angles and complex geometries. However, not all parts require 5th axis milling, in fact, 3rd axis milling is suitable for most basic parts. The number of necessary axes depends on the job, and is a direct correlation of the mills’ capability to machine multi sided parts. In industries such as aerospace, medical, firearms, defense, & OEM, tight tolerances and complex geometries have become the norm, meaning CNC milling isn’t going anywhere. The technologies’ capacity to create intricate and custom designs, while maintaining consistency and accuracy, has expanded the possibilities for innovation and product development. Ultimately enabling manufacturers to craft parts with intricate curves, and compound angles, that may have been seen as impossible in recent years.